(Part Two of the story of the Grumman Canoe that played a key role in Ely’s tourism history and how the Boundary Waters came to be known as canoe country).
Metal, stretching and drilling jigs
Rolls of 5052 grade aluminum arrive at the factory with a hardness rating of “O.” The hardness rating is an engineering specification with O being the softest. The rating increases in tensile strength from O, which is a soft, malleable aluminum.
Baking the aluminum to a high temperature increases the tensile strength and hardness rating to a T-3, T-4, or T-6 at least for aluminum. After baking to a specified time and temperature of 750 degrees for 12 hours, the aluminum used in the canoe transforms to a tensile strength of T-4. The increase of tensile strength and hardness gives aluminum its superior strength-to-weight ratio.
Once the first set-up is complete for a certain length canoe, like the 13-footer being fabricated the day I was there, many sheets of the O aluminum are formed for that length, to be efficient. The two lengthwise halves are formed separately by a specialized stretching machine with a die in the shape of a canoe half.
After coming off the flattening roller and being cut to size by a shear, the canoe length sheet is placed over the die and attached to jaws that hold the edges tightly. Then, hydraulically lowering the table slightly, moving it with a slight rotation, wraps the aluminum around the die, stretching it, forming the canoe half. Extra length is added for attaching to the forming machines and will be trimmed after the forming process.
The halves will be hand-drilled in a jig after forming. They are mounted to a drilling jig, the canoe’s exact pattern and shape. The holes in the jig are a precise diameter and the drill bit simply follows the jig holes into the attached aluminum.
After removing the formed half of the canoe from the jig the excess metal is trimmed and then it moves to the oven for baking. A piece of O aluminum with a thickness of .050 can be folded in half without breaking. It will easily form around a wooden block, die, or mold. After heat treating, this becomes impossible; it will crack.
A small piece of metal fabricated into a rib, bulkhead, or similar piece is positioned within a form and placed on a press. As the press lowers onto the aluminum, it takes up the contour and shape of the forming block.
We watched while the Grumman logo G was formed in the forward bulkhead. There is no loud noise or banging or anything like that; all we could hear was the electric motor humming with the soft sounds of a hydraulic ram barely moving.
Riveting and rivets and bucking. Nathasha and I were walking along the factory floor, crossing over air hoses connected to the rivet guns and air drills. The sounds of quiet, high-speed buzzing and whirring of the air drills were often overcome by the loud brrrp, brrrp of the rivet gun. I put my earplugs back in, the type made of soft silicone, which slide in quickly.
Rivet guns are built with an internal hammer driven by air pressure, and mounted in the barrel is a tourished face, or the flat shape of the counterpeen with a sunk rivet head. The rivets are made of aluminum, of a certain alloy. They have a manufactured head which is either a rounded protruding head called a universal head, or a flat head style called a countersunk head fitting flush into a countersunk drilled hole. The opposite end of the rivet, the end that will be bucked or formed, is called the shop head, or formed head. A short heavy bar of steel or other heavy metal that fits in the palm of your hand is called a bucking bar. While holding the bucking bar the shop head forms as the peen hammers the manufactured head. The vibrations travel through the shank of the rivet causing the metal bucking bar to act like an anvil, thus expanding the shank of the rivet forming a watertight seal by filling the entire hole drawing the metal tight. This is called bucking a rivet and that is how a bucktail is formed. The shop head or bucktail is the part you see when looking along the inside of the canoe and it looks like a small button. The exact diameter and length of the rivet are important to form the proper size bucktail. Two people working as a team, one with the rivet gun and the other holding the bucking bar against the protruding rivet shank. If you buck a rivet too long, it will destroy the shop head by flattening it. There are specific requirements for the size of the formed shop head, the bucktail. If these are not met, the rivet will be drilled out and replaced, and then the hole will be upsized since the precisely drilled rivet hole is stretched out of dimension. If the bucking bar slips off while bucking the rivet, the skin will be marred or dented by the peen since all the force is now hammering on the aluminum skin. Next time you fly, look across the top of the airplane wing at the smoothness of the countersunk rivets securing the skin; you will see no deformities. Proper drilling and riveting allow extreme forces such as air loads or water loads in a canoe, to transfer to the structure, preventing the aluminum from cracking under a flexing load. This is why the skins are not welded. The same craftsmanship found in aviation is built into the Grumman canoe.
What caught my eye were the racks of different forms for the different lengths of all the canoes and all the different shapes and forms for the many structural components that make up the canoe. The racks and shelves are labeled with the canoe sizes marked on shelves in yellow tape. After seeing all of these shelves with forms, pieces, and parts for each size canoe I took a short breath as I realized every canoe that I touched at the outfitter and even all the old Grumman canoes floating around Ely and the BWCA, each one of those canoes built in the 50s and 60s, seventies and up until today are still formed and fabricated right here on the same concrete floor in the same building where I am now standing. That is over 70 years and tens of thousands of canoes. The same machines, same forming blocks, and even the same rail spur for the boxcars stacked to the top with canoes heading west and to Ely.
Many of those canoes arrived on the west end of town by rail, near the old metal buildings, long before Babe’s Bait and the Dollar Store. After the boxcars arrived, it took a couple of days dismantling the attached wooden blocking by pulling nails and separating the bracing between the canoes with crowbars. Finally sliding them out and down the embankment and flipping them onto our shoulders. The padded yokes would be installed later. After portaging them to the trailer, we sent them up Sheridan Street. Just think, after traveling over a thousand miles by rail without touching water and finally landing in their new home, the back-alley yard of Bill Rom’s Canoe Country Outfitters, the largest Grumman dealer in America.
(Next week: Part three of the story of the Grumman Canoe).
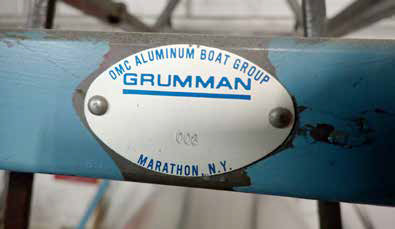
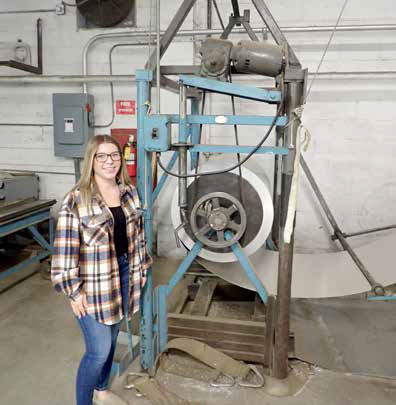
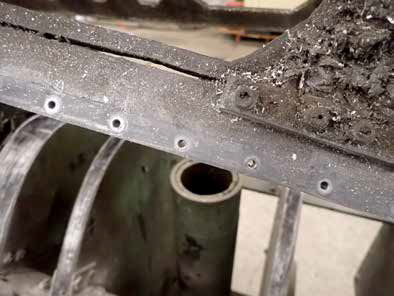
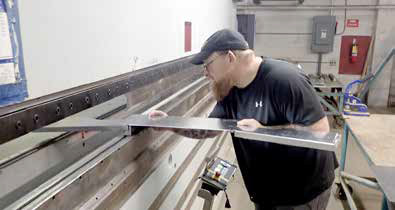
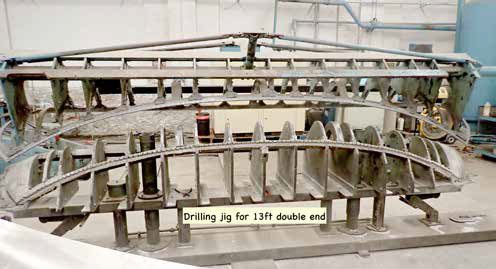
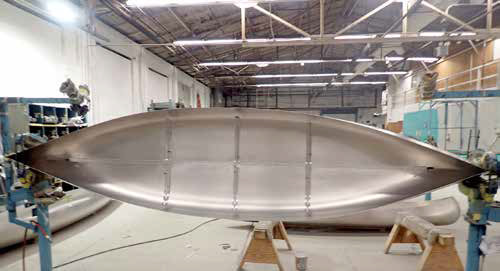
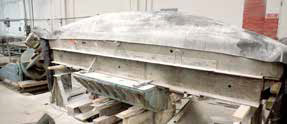
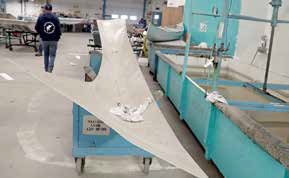
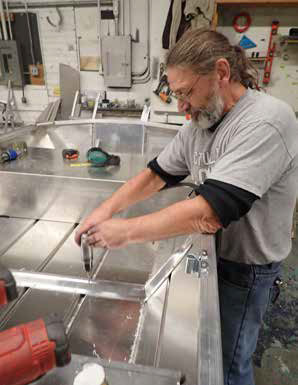
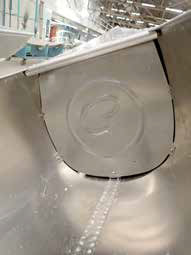
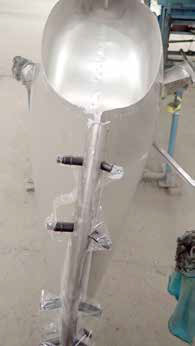